The right manufacturing workflow software optimizes your production process and improves communication among your team. And in today’s manufacturing industry, ensuring your workflows support your business growth is more important than ever.
With so many manufacturing workflow management software on the market, it can be challenging to know which one is right for you.
This comprehensive guide will put you on the right track to finding the best option among the top 10 manufacturing workflow software this year.
What is a manufacturing workflow?
A manufacturing workflow is a process by which products are created.
This includes anything from designing and creating prototypes to manufacturing and assembling products.
The most common types of manufacturing workflows include:
- Prototyping — This involves creating prototypes of products to test their feasibility and functionality. This is often done in the early stages of product development before manufacturing begins.
- Design to Manufacturing — In this workflow, designs are created and sent to manufacturers for production. You may use this workflow type for mass production or when speed is a priority.
- Assemble to Order — In this workflow, products are only assembled after customers order them. This helps reduce inventory costs and speeds up delivery times.
What is manufacturing workflow software?
Manufacturing workflow software is a system that helps manufacturing businesses manage and optimize their workflows.
With the right manufacturing workflow management software, businesses can:
- Automate tasks.
- Improve communication and collaboration among team members.
- Optimize the production process.
Benefits of workflow software in manufacturing
Workflow software offers many benefits for businesses in the manufacturing industry. Below are some of the most important ones.
1. Increased efficiency
With the help of manufacturing workflow management software, businesses can automate tasks and improve communication among team members.
This leads to increased efficiency and optimized production processes.
2. Improved collaboration
When team members can easily communicate and collaborate, it leads to faster turnaround times and improved quality control.
Workflow software allows team members to share files, comments, and tasks with each other.
3. Reduces costs
Manufacturing workflow management software reduces costs by optimizing production processes.
In addition, many workflow software programs allow businesses to track their spending, so they can identify where they can save money.
4. Improved customer satisfaction
Businesses can improve customer satisfaction by reducing manufacturing lead times and increasing production efficiency.
In addition, many workflow software programs allow businesses to track customer orders and feedback, so they can quickly address any issues that may arise.
What are the components of an ideal manufacturing workflow software?
Not all manufacturing workflow software programs are created equal.
The best manufacturing workflow management software is:
- Easy to use and intuitive — Its design allows you to navigate the various features easily.
- Flexible — Choose a solution that you can personalize to meet the specific needs of your business.
- Scalable — Ensure your chosen software can grow with your business. It should offer features that allow you to add more users and expand functionality as your business grows.
- Integrated — Seamless integration with other software programs allows you to simplify your production process and avoid data silos.
- Customer-oriented — When things go wrong, it’s essential to have a team of customer support experts who can troubleshoot the issue and get back on track. The best manufacturing workflow software programs offer 24/7 customer support.
How we chose the best manufacturing workflow software
To help you find the best manufacturing workflow software, we looked at various factors, including features, pricing, customer support, and integrations.
We also considered the specific needs of businesses in the manufacturing industry, such as:
- The ability to automate tasks.
- Improve communication and collaboration among team members.
- Optimize the production process.
The 10 best manufacturing workflow software
Below are the best manufacturing workflow management software solutions:
1. Method CRM
Key features
- QuickBooks and Xero two-way sync, so your financials are always up to date.
- Online customer portal for an improved customer experience.
- Mobile app to keep you in the loop anytime, anywhere.
- Custom reporting based on your business needs.
- Native integrations with Gmail, Outlook, Mailchimp, Zapier, and more.
Pros
- Save time and enhance accuracy when you sync customer data between Method CRM and QuickBooks or Xero.
- Reusable templates to personalize emails, reports, invoices, estimates, and more.
- No code, unlimited customization to create a tailored solution.
- The ability to automate your business all around.
Cons
Method CRM is currently only available in English to users of QuickBooks or Xero.
Pricing
Method offers three subscription options:
- Contact Management: $25 per user per month.
- CRM Pro: $44 per user per month.
- CRM Enterprise: $74 per user per month.
Method CRM is rated the #1 CRM by QuickBooks and Xero users. Watch the free demo to find out why.
2. Prodsmart
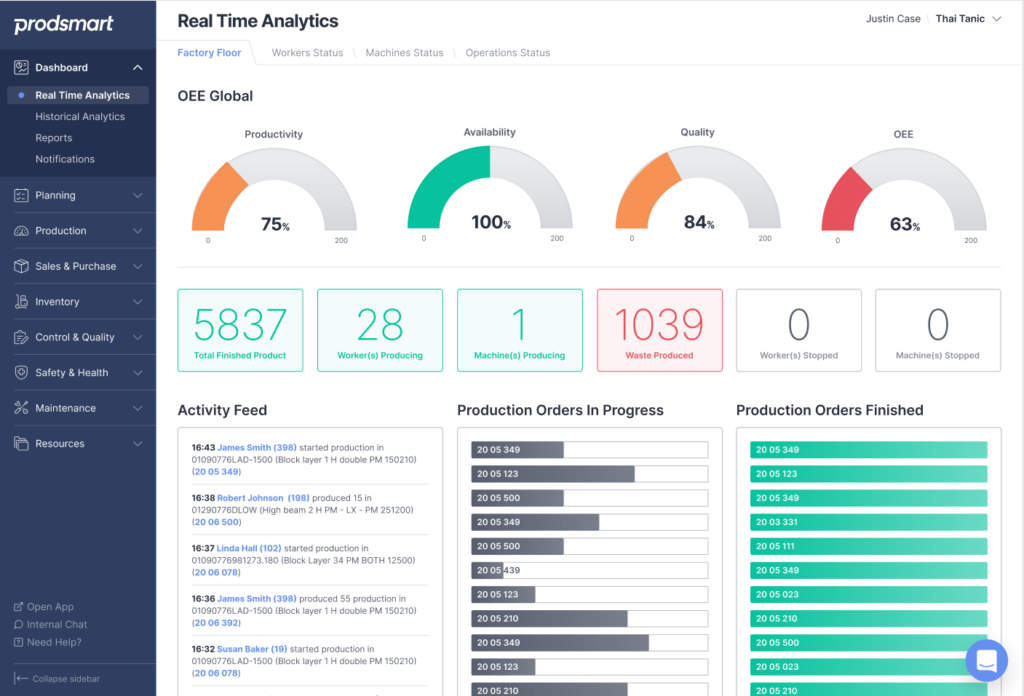
Image credit: Prodsmart
Key features
- Real-time operations tracker.
- Scheduling and material requirements planning.
- Inventory management.
Pros
- Simple to use and intuitive interface.
- Very responsive customer success team.
- Accurate tracking and inventory overview.
Cons
Some users have pointed out a lack of warehouse management system features, which are a must-have for some manufacturing companies.
Pricing
Prodsmart offers a single annual pricing plan for $9,925 per year and a 14-day free trial.
3. Katana Manufacturing ERP
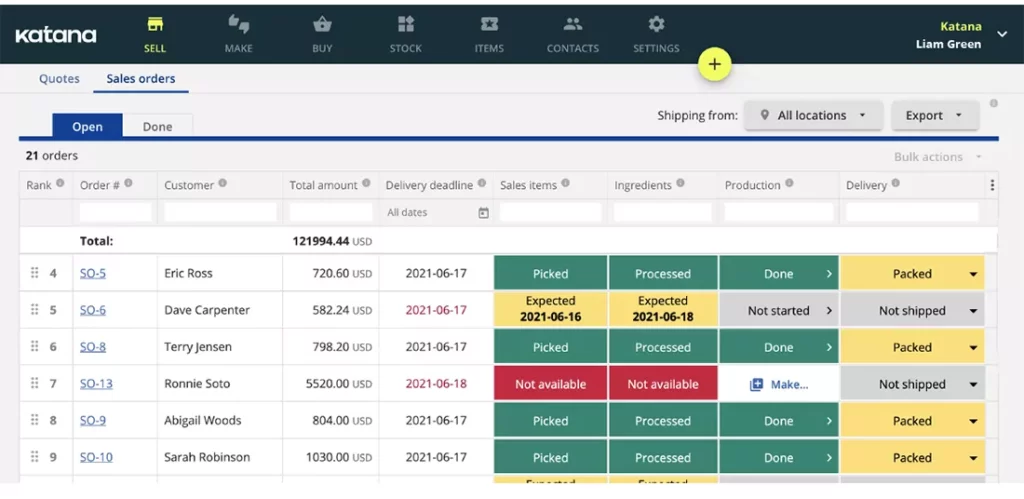
Image credit: Katana MRP
Key features
- Live inventory management.
- Purchase order management.
- Open API integrations (with Zapier).
Pros
- Easy to use and implement.
- Comprehensive manufacturing and inventory solution.
- Reliable integration engine.
Cons
Less affordable than most competitors, especially for smaller businesses.
Pricing
Katana MRP offers three subscription options:
- Essential: $99 per month billed annually.
- Advanced: $299 per month billed annually.
- Professional: $799 per month billed annually.
Katana also offers a free 14-day trial, no credit card required.
4. L2L Smart Manufacturing Platform
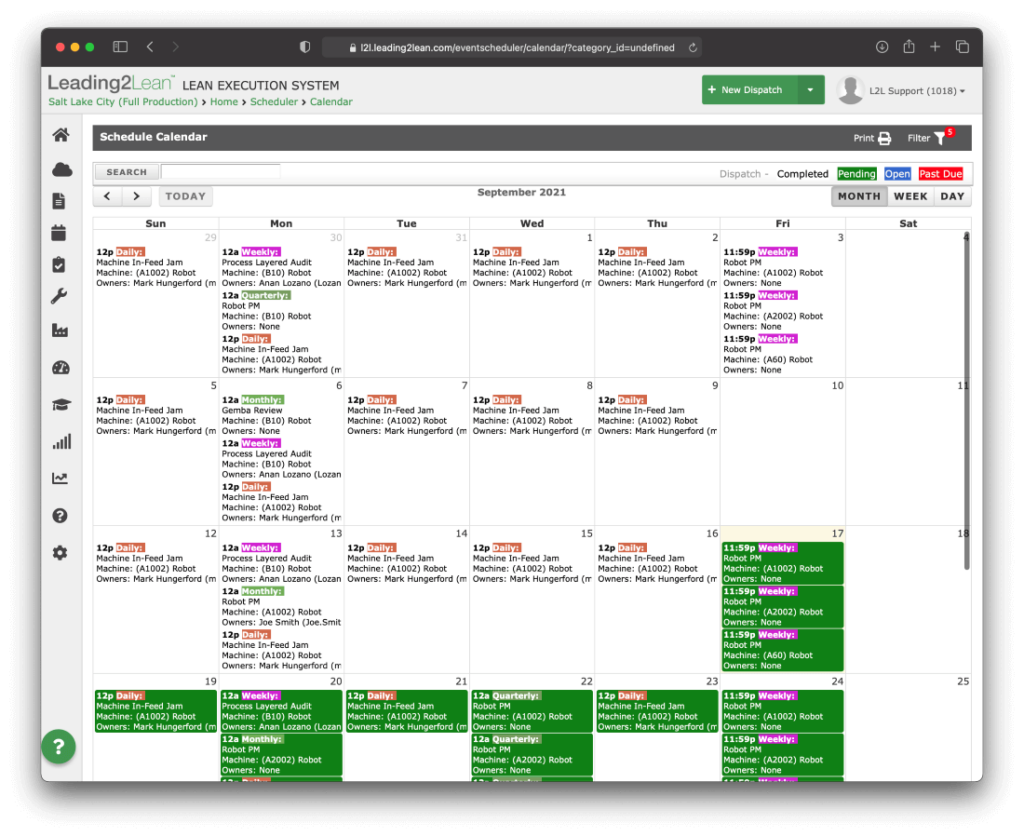
Image credit: L2L
Key features
- Production management.
- Scheduling and work orders.
- Customized reporting.
Pros
- Accessible and easy to implement.
- Quick and efficient tech support team.
- Accurate data analytics.
Cons
Some users have reported that recurrent system updates hinder operations.
Pricing
L2L does not offer any fixed pricing plans or a free trial period.
5. Genius ERP
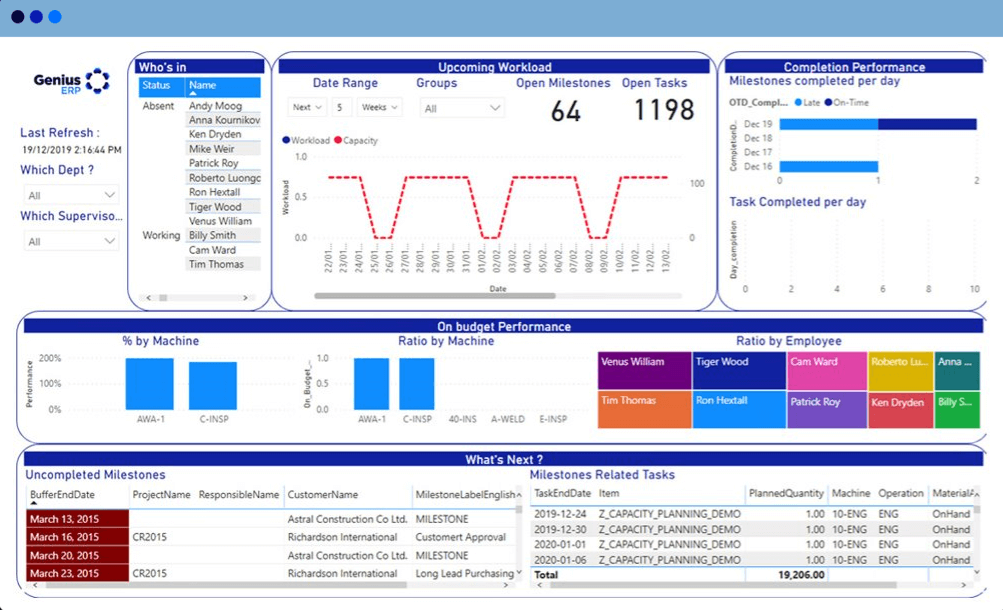
Image credit: Genius ERP
Key features
- Shop floor scheduling.
- Vendor and inventory management.
- Production planning and reporting.
Pros
- Easy to use and implement.
- Centralized view of the manufacturing process.
- Automated quote to purchase order conversion.
Cons
Some users have reported a shortage of formulating quantities and built-in analytical tools. Reporting capabilities are too limited for some manufacturing businesses.
Pricing
Genius does not offer any fixed pricing plans or a free trial period.
6. SyteLine
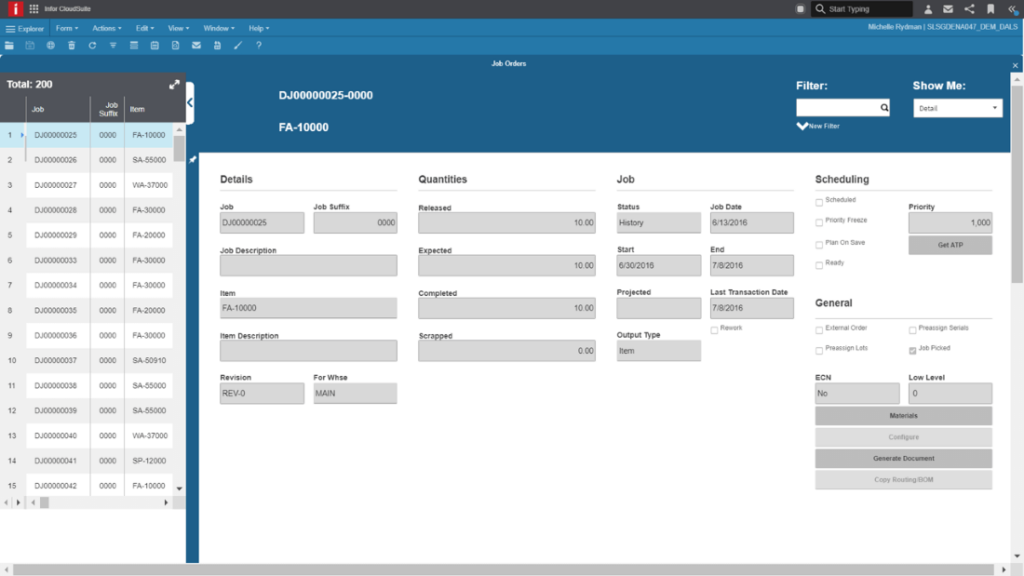
Image credit: Infor SyteLine
Key features
- Operations planning and scheduling.
- Supply chain management.
- Collaboration portals for customers, vendors, and resellers.
Pros
- Intuitive user interface.
- Strong integration with Microsoft Excel.
- Real-time order processing and tracking.
Cons
Users have reported slow loading speeds and significant limitations surrounding reporting.
Pricing
SyteLine has no fixed pricing plans or a free trial period.
7. ProntoForms
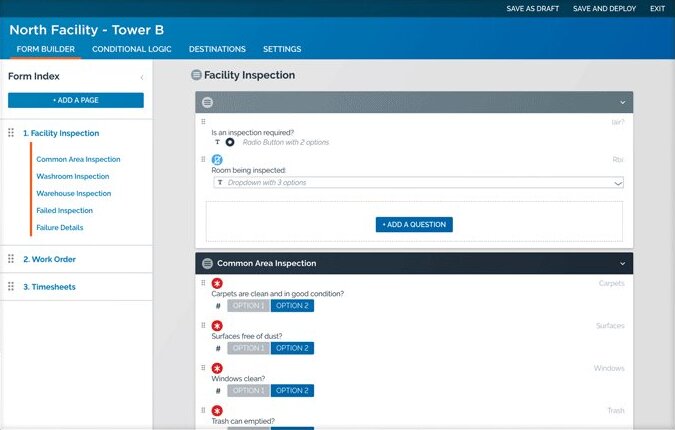
Image credit: ProntoForms
Key features
- App and form builder.
- Workflow creation and automation.
- Integrations manager.
Pros
- Automated data distribution rules.
- Simplified bulk-dispatch.
- Easy and intuitive navigation.
Cons
Some users have shared their frustration with tech support sometimes taking too long to fix issues and that the software is hard to implement without help.
Pricing
ProntoForms offers three subscription options:
- Essentials: $15 per user per month.
- Advanced: $45 per user per month.
- Enterprise: Custom pricing.
ProntoForms also offers a free trial for an undefined period.
8. Infor VISUAL
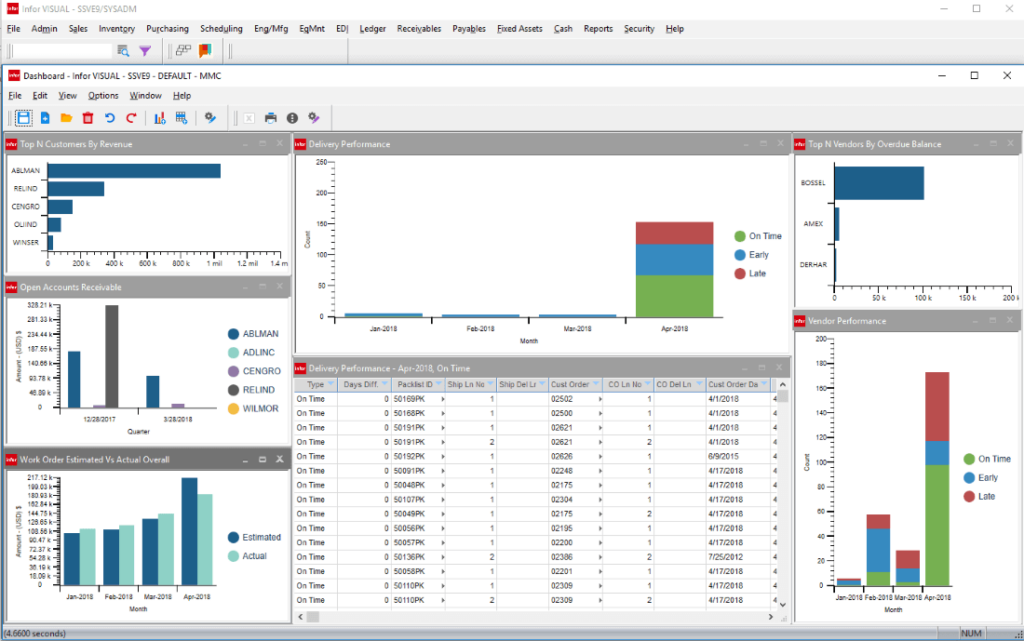
Image credit: Infor VISUAL
Key features
- Capacity planning.
- Serial number tracking.
- Estimate creation.
Pros
- Fully customizable across available features.
- Centralized data view.
- Intuitive reporting and insights.
Cons
Requires a high level of customization for it to become a beneficial tool. Most users have reported the need for an implementation partner.
Pricing
Infor VISUAL has no fixed pricing plans or a free trial period.
9. S2K Enterprise
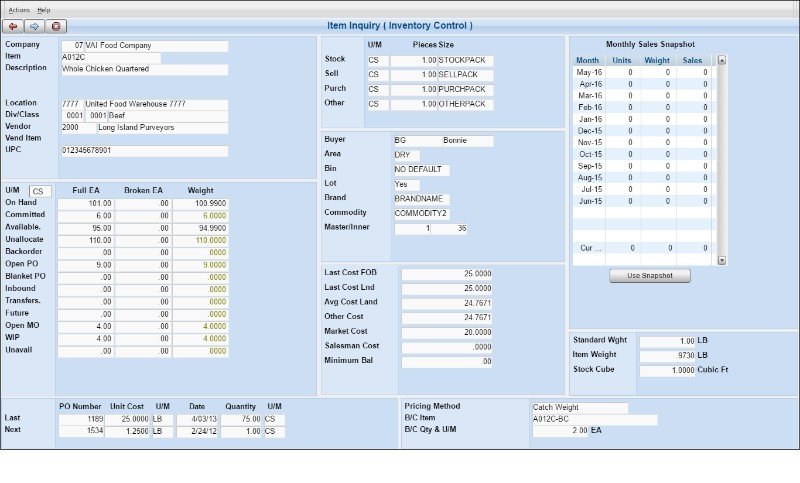
Image credit: Vai S2K
Key features
- Manufacturing work orders.
- Material requirement planning.
- Shop floor control.
Pros
- Versatile and customizable.
- Affordable ERP solution.
- IBM-based system.
Cons
S2K Enterprise is not a cloud software solution. Many users have reported that the solution is difficult to implement without a dedicated manager or consultant to help.
Pricing
S2K Enterprise has no fixed pricing plans or a free trial period.
10. Microsoft Dynamics ERP
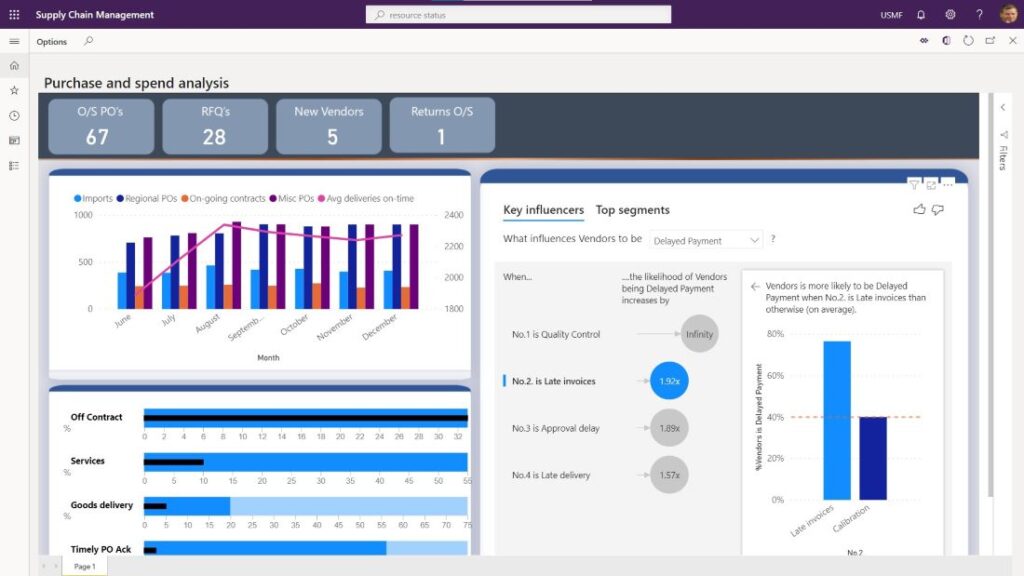
Image credit: Microsoft Dynamics
Key features
- Warehouse inventory management.
- Barcoding and label printing.
- Real-time tracking and traceability.
Pros
- Easy to use and deploy.
- Increased productivity and reduced sales cycle.
- Full integration with Microsoft products.
Cons
Too broad a solution, so it may not be the best fit for smaller, niche manufacturers.
Pricing
Dynamics 365’s Supply Chain pricing plan starts at $180 per user per month. A 30-day free trial is available.
Which manufacturing workflow software should you use?
The manufacturing workflow software you choose will ultimately depend on the specific needs of your business.
If you’re looking for a comprehensive solution that covers all aspects of the manufacturing process, Method CRM is your best bet.
With Method CRM, you’ll get a centralized view of your entire manufacturing workflow, from quote to purchase order to invoice.
You can also track and manage your inventory, schedule and dispatch work orders, and generate custom reports.
In the video below, check out how an integration with Method helped double this shipping container company’s revenue in just three years.
Manufacturing workflow software FAQs
What is workflow automation in manufacturing?
Workflow automation in manufacturing is the use of software to automate and manage manufacturing processes. This can include tasks such as quote to purchase order conversion, work order creation and dispatch, and invoicing.
What is a good workflow tool?
A good workflow tool meets the specific needs of your business. When choosing manufacturing workflow software, you should prioritize features that can automate your processes as your business grows and evolves.
What is an example of a manufacturing workflow?
A typical manufacturing workflow includes:
- Quote creation and purchase order processing.
- Work order creation and dispatch.
- Inventory management.
- Quality control.
- Shipping and logistics.
- Invoicing.
- Reporting, and analytics.
Begin improving your manufacturing workflow by watching a free demo of Method, the #1 CRM by QuickBooks and Xero users.
Photo credit: Sam Moghadam Khamseh via Unsplash